Alright, so it was finally time to get this engine on the dyno. Spent ages putting it together, tinkering here and there, but you never really know what you’ve got until you strap it down and measure it properly.

Getting Started
First thing was actually getting the lump onto the engine stand. It’s always a bit of a wrestle, heavier than it looks. Had to make sure it was bolted down securely to the dyno adapter plate. Checked those bolts like three times, didn’t want anything coming loose later. Then came connecting the driveshaft from the dyno absorber itself to the flywheel. You gotta get that alignment spot on.
Before even thinking about firing it up, went through the basic checks:
- Oil: Filled it up, checked the level. Fresh stuff.
- Coolant: Topped off the system connected to the dyno’s cooling tower. Made sure there were no air pockets, best I could tell.
- Leaks: Quick visual scan for anything dripping already. So far, so good.
- Wiring: Made sure the basic ignition wiring was hooked up and secure.
Hooking Everything Up
This part takes a bit of time. Connected the big radiator hoses from the engine to the dyno’s cooling system. Then the fuel lines – connected my fuel tank with the right pump pressure going to the carb or injectors. The exhaust was next, hooked up the shop’s exhaust extraction pipes right over the headers. You don’t want to be breathing that stuff in for hours.
Then came the sensors. This is crucial. Plugged in the oil pressure sensor, water temperature sensor. Rigged up the RPM pickup, usually off the crank trigger or coil. Wideband O2 sensor went into the exhaust collector. Connected the dyno’s throttle actuator to the linkage. Finally, hooked up all the dyno’s own measurement sensors and the main control harness.
The First Fire-Up
This is always the slightly nervous bit. Double-checked everything looked okay. Turned on the fuel pump, checked for leaks again. Hit the starter. It coughed a bit then roared to life. Instantly listening for any bad noises, watching the oil pressure gauge jump up. Let it idle, warming up slowly. Kept an eye on temperatures, looking for leaks again. Made sure the throttle control was responding.
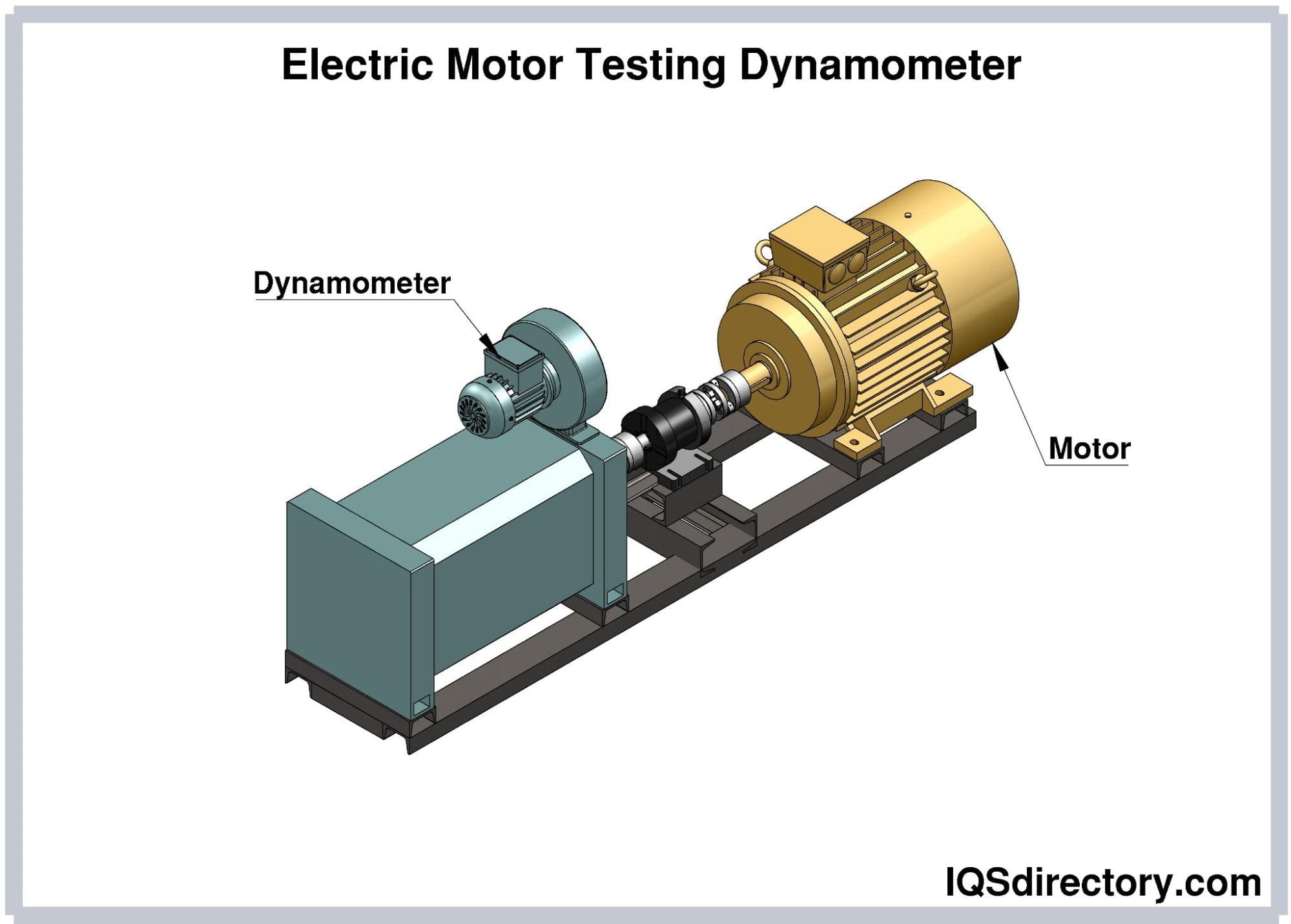
Making Some Noise – The Actual Testing
Once it was up to temperature and sounded happy, we started easy. Put a very light load on it using the dyno absorber, just let it run steady at a low RPM for a bit. Then, started doing some gentle sweeps up and down the RPM range, still under light load. Everything seemed okay.
Time for the real runs. We decided to do some steady-state tests first. Hold the engine at specific RPM points, like maybe 3000, 3500, 4000 RPM and so on, applying enough load to hold it steady, and record the power and torque figures. This gives you good data on specific points.
Then, the power pulls. Started the data recording, loaded the engine lightly at a low RPM, maybe 2500 RPM, then smoothly opened the throttle wide open while the dyno controlled the acceleration rate, sweeping it all the way up to the redline. You really hear it sing then, and feel the torque through the whole setup. Did several pulls like this to make sure the numbers were consistent. Watched the air/fuel ratio on the wideband display during the pull.
Looking at the Results
The dyno computer screen shows the graphs right away – torque curve, horsepower curve. We printed out the results after the main runs. You can immediately see where it makes peak power, peak torque, and how smooth the curves are. Compared it to previous tests if you have them, or just analysed if the changes made had the desired effect.
Shutting Down
After the last pull, let the engine run for a bit with no load to cool down evenly. Then shut it off. Did one last walk-around, checking for any new fluid drips or anything that looked stressed. Disconnected the fuel pump and battery.

Packing up always feels good after a successful session. The dyno doesn’t lie. Sometimes the numbers are great, sometimes they tell you need to go back to the drawing board. Either way, you know exactly where you stand. Definitely worth the effort to get real data.